Our
CIP (Clean-In-Place) Skid
Custom Solutions for Food and Beverage CIP Systems
NAW invented CIP, and we’ve been innovating ever since. Our teams will work with you to custom-engineer a CIP system to meet your specific requirements and select the appropriate solutions from our portfolio of CIP cleaning chemicals. This tailored approach optimizes your production and delivers operational efficiencies.
Optimized CIP processes efficient use of resources means reducing the amount of water, energy and chemistry you use.
- Home
- CIP (Clean-In-Place) Skid
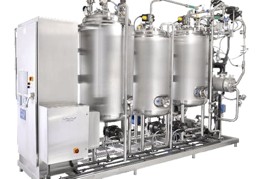
CIP (Clean-In-Place) Skid
Clean-In-Place (CIP) systems are automated systems used to clean the interior surfaces of food and beverage process pipes, processing vessels, tanks, spiral freezers, mixers, blenders, homogenizers, roasters and associated fittings, without disassembling the process. Thorough, repeatable in-place cleaning is critical to the quality of your product, the safety of consumers—and your bottom line.
NAW CIP Systems are engineered to your specific plant application, layout and utility requirements for effective and efficient sanitary process equipment cleaning. Our application-specific CIP design and sizing ensures sufficient flow. As a result, appropriate pressure is available to thoroughly remove residue, rinse effectively, shorten cycle times and promote worker safety.
Our in-house automation programming experts design each CIP program to optimize cycle times that get you back into production faster, while reducing chemicals, water use and operating costs.
NAW CIP Systems are sanitary and can be engineered to meet 3-A standards.
Materials
Stainless Steel: High-grade stainless steel (304/316) for durability, corrosion resistance, and ease of cleaning.
Plastic Components: Food-grade and chemical-resistant plastics for internal parts.
Rubber Seals: Durable, chemical-resistant rubber seals to ensure leak-proof operation.
Control Panels: Stainless steel or powder-coated metal for robust, easy-to-clean surfaces.